The Art of Assembly: Where Data Engineering Meets Conveyor Belts
Manufacturing is all about being efficient and getting the most out of automation, solid processes, skilled workforce, and especially data. Data helps drive the decisions that keep everything running smoothly.
In this blog, we’re going to explore how data plays a vital role in manufacturing. From the sensors on machinery that monitor everything in real time, to tracking how well different stages of the production line are doing, to managing the supply chain – data is at the centre of it. We’ll see how data can help prevent machine breakdowns, drive efficiencies in production lines and maintain high product quality. Let’s see what’s involved in using data to drive manufacturing efficiencies.
Data in manufacturing
Manufacturing thrives on efficiency. Efficiency drives productivity. Improved productivity leads to a lower unit production cost, which is the main goal here. The best production lines seamlessly combine automation, clever processes, and human expertise to drive this efficiency. And data sits behind it all. Data is absolutely crucial at informing decisions that drive modern production efficiencies and improve productivity. Let’s explore what’s involved.
Machinery sensors: Modern manufacturing equipment is often outfitted with numerous sensors that monitor everything from temperature and pressure to vibration and speed. These sensors generate continuous streams of data, providing a real-time look into machine performance and operating conditions.
Production line outputs: Every stage of the production line is a source of data. This includes data on production volumes, processing times, and waste quantities. Monitoring these outputs helps in assessing the efficiency of production lines and identifying areas for improvement.
Supply chain logistics: Data from the supply chain includes inventory levels, material flow, delivery times, and supplier performance. Integrating this data helps in optimising inventory management, reducing lead times, and improving just-in-time delivery systems.
Data driving manufacturing efficiencies
As we can see, manufacturing companies collect vast amounts of data from various sources. This data can be used for predictive maintenance, optimising production processes, and ensuring product quality. The less disruption and wastage that a production line has, the more productive it is.
Real-time data, in particular, plays a critical role here. It allows manufacturers to make immediate adjustments to production lines, supply chain disruptions, and quality control as issues are detected. The sooner you can detect and act upon the arising issues, the less downtime the factory will suffer (if any). Less downtime means lower unit cost of production.
Predictive maintenance: By analysing data from machinery sensors, manufacturers can predict when equipment might fail and perform maintenance before breakdowns occur. This proactive approach not only saves costs associated with downtime but also extends the life of the equipment.
One of our clients was able to implement this approach after switching to IOblend’s real-time data processing capabilities. They moved from a static weekly batch job to real-time streaming data straight from the sensors. This allowed them to put in place predictive maintenance analytics, which led to significantly reduced machine stoppages.
Optimising production processes: Data analytics enable manufacturers to refine production processes. For instance, by analysing the data collected from production line outputs, companies can identify inefficiencies or deviations from the norm. They can then make improvements to the throughput and reduce cycle times.
If sensors detect a product defect or a drop in machine performance, the production line can be adjusted in real-time. Supply chain disruptions can be predicted ahead of time to minimise plant stoppages. And so on.
Quality control: Advanced data analytics are used to enhance product quality. For example, image recognition technologies powered by AI can detect defects that are not visible to the human eye. Similarly, statistical process control techniques use data to ensure that the manufacturing process remains within predefined quality standards.
Real-time monitoring systems can immediately alert personnel to quality issues during production. This allows for instant corrective measures, reducing the cost and time associated with post-production quality checks and product recalls.
Challenges with manufacturing data management
One of the principal data challenges within the manufacturing sector lies in the integration and management of it. Many manufacturing plants operate on legacy systems that are not designed to communicate with one another. Even modern ones. Integrating these systems with data analytics tools is often a significant challenge. This usually means substantial financial investment and technical effort by experienced data engineers and data scientists.
The management of data itself is no less painful. The sheer volume and variety of data generated in a manufacturing environment can overwhelm traditional data processing systems. Moreover, ensuring the accuracy and consistency of data across various sources adds a whole other layer of complexity. Remember, most of this data from sensors and machinery is low-latency real-time. Data governance practices need to be robust to maintain data integrity on-the-fly, which is crucial for generating reliable insights.
Cost considerations
Financially, the cost of upgrading systems, implementing new data management software, and maintaining these systems can be considerable. Many manufacturers keep their legacy systems for a very long time because of the this. We have seen some really clunky implementations with technologies that mutated over the years as new requirements arose. Few people even remembered what the logic was in the first place. It was costing them a fortune to run and maintain. And they couldn’t get half the insights they needed from this architecture.
Some larger manufacturing firms can spend millions annually on data management solutions alone. On top of the license outlays, there is also the manual effort involved in overseeing these data systems. Despite advances in automation, significant manual effort is still required with lots of the solutions. Particularly in data cleansing and preparation, which are critical for accurate data analysis. The longer they spend on data prep and wrangling, the less efficient the production line is.
Manufacturing margins are too narrow to ignore such inefficiencies with their data processes. Not only do they run an expensive data stack, but they also add to the risk of plant disruption. Consider this: a week-long delay in spotting an issue with the production line can cost millions.
Strategies to improve decision-making in manufacturing
Remember, manufacturing is all about efficiency. You must keep your production costs to an absolute minimum – that’s the Holy Grail of manufacturing. Cost pressures are ever-present – raw materials, people’s wages, regulations – all go up over time. It’s critical to gain better efficiencies across all aspect of production to maintain or improve margins. And the best way to achieve is through a clever application of data, systems, and human expertise.
Technological integration: One consideration should be the investment in systems that can interact and integrate seamlessly in real-time. This includes adopting platforms that support the IoT to gather data from equipment sensors, assembly lines, and products in transit. These systems must not only collect data but also facilitate its easy aggregation and analysis.
To truly harness the power of collected data, manufacturing firms should implement advanced analytics and machine learning algorithms. These technologies can analyse patterns in vast datasets to predict equipment failures, optimise production schedules, and improve supply chain logistics. There is a big efficiency gain in having predictive capabilities from what we have seen in practice (easily seven figures).
Organisational change: Data insights are only as good as the people who use them to make decisions. So, it’s essential for manufacturing companies to foster a data-driven decision-making culture across their organisations. At all layers.
Now, this is more easily said than done, as human intuition or tradition are hard to overcome. Especially in long-established manufacturing settings, where employees could have spent decades of their careers. They can do their jobs with eyes closed. Why would they want to suddenly do things “as the computer says”? They wouldn’t.
But it is essential to get them to trust the data to gain better production efficiencies. You need to find a right balance where data is the driving force yet still steered by the human expertise. And take them on the data journey with you, showing the benefits one production step at a time.
Equipping your staff with the skills to interpret and leverage data easily will help immensely. This might take a form of regular training sessions, workshops, and courses. Design them to help your employees understand how to use data analytics tools and interpret insights. Never make these sessions too technical, however. You want to empower your staff, not overwhelm them with the tech jargon so they lose patience and interest.
Beyond training, giving your employees access to real-time data and analytics tools can enhance decision-making at the operational level. This approach helps decentralise decisions and allows for quicker responses to production challenges. Make sure you give them the right tools that are easy to use and deliver relevant information. If data isn’t seen as something difficult to use and interpret, the employees will adopt its usage much more readily.
Strategic partnerships: Don’t shy away from seeking external assistance. Forming strategic partnerships with technology providers can offer numerous benefits. These providers can offer solutions tailored to your specific manufacturing needs and integrate these solutions with the existing systems.
Technology partners often bring industry-specific knowledge that can be helpful for navigating the unique challenges of manufacturing. They can advise on best practices, help comply with industry regulations, and suggest ways to improve efficiency and productivity. They can also provide valuable training and support.
Given the fast pace of technological advancement, partnering with tech providers ensures that manufacturing systems stay up-to-date and deliver efficiencies.
Start your manufacturing data journey
The hardest step to take is always the first. But the benefits by far outweigh the challenges if you follow the right strategy. By integrating cutting-edge technologies, fostering a culture of data literacy, and forming strategic partnerships, your decision-making processes will greatly improve. This will lead to greater manufacturing efficiencies. Remember, your competitive advantage stems from efficient production.
At IOblend, we are always keen to support the manufacturing sector. Our solution is especially well-suited to handle low-latency real-time and diverse production data demands. And it is very flexible to suit pretty much any manufacturing setting in a cost-efficient manner. Get in touch today and let’s see how we can help your business.
IOblend presents a ground-breaking approach to IoT and data integration, revolutionizing the way businesses handle their data. It’s an all-in-one data integration accelerator, boasting real-time, production-grade, managed Apache Spark™ data pipelines that can be set up in mere minutes. This facilitates a massive acceleration in data migration projects, whether from on-prem to cloud or between clouds, thanks to its low code/no code development and automated data management and governance.
IOblend also simplifies the integration of streaming and batch data through Kappa architecture, significantly boosting the efficiency of operational analytics and MLOps. Its system enables the robust and cost-effective delivery of both centralized and federated data architectures, with low latency and massively parallelized data processing, capable of handling over 10 million transactions per second. Additionally, IOblend integrates seamlessly with leading cloud services like Snowflake and Microsoft Azure, underscoring its versatility and broad applicability in various data environments.
At its core, IOblend is an end-to-end enterprise data integration solution built with DataOps capability. It stands out as a versatile ETL product for building and managing data estates with high-grade data flows. The platform powers operational analytics and AI initiatives, drastically reducing the costs and development efforts associated with data projects and data science ventures. It’s engineered to connect to any source, perform in-memory transformations of streaming and batch data, and direct the results to any destination with minimal effort.
IOblend’s use cases are diverse and impactful. It streams live data from factories to automated forecasting models and channels data from IoT sensors to real-time monitoring applications, enabling automated decision-making based on live inputs and historical statistics. Additionally, it handles the movement of production-grade streaming and batch data to and from cloud data warehouses and lakes, powers data exchanges, and feeds applications with data that adheres to complex business rules and governance policies.
The platform comprises two core components: the IOblend Designer and the IOblend Engine. The IOblend Designer is a desktop GUI used for designing, building, and testing data pipeline DAGs, producing metadata that describes the data pipelines. The IOblend Engine, the heart of the system, converts this metadata into Spark streaming jobs executed on any Spark cluster. Available in Developer and Enterprise suites, IOblend supports both local and remote engine operations, catering to a wide range of development and operational needs. It also facilitates collaborative development and pipeline versioning, making it a robust tool for modern data management and analytics
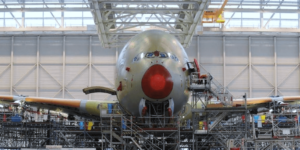
The Art of Assembly: Where Data Meets Conveyors
Manufacturing is all about getting the most out of automation, skilled workforce, and data. Data helps drive the decisions that keep everything running smoothly
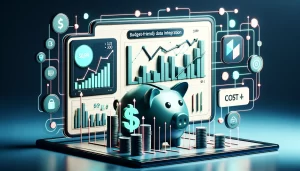
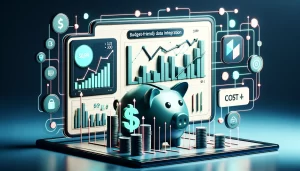
Saving Cents on Data Sense: Less Cost, More Value
No company is immune from the pains of data integration. It is one of the top IT cost items. Companies must get on top of their integration effort.
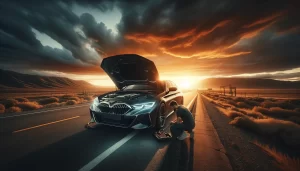
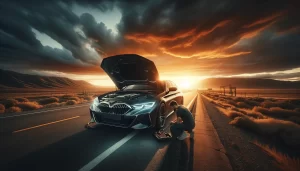
Operational Analytics: Real-Time Insights That Matter
Operational analytics involves processing and analysing operational data in “real-time” to gain insights that inform immediate and actionable decisions.
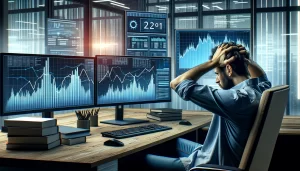
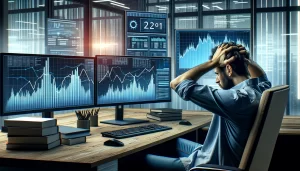
Deciphering the True Cost of Your Data Investment
Many data teams aren’t aware of the concept of Total Ownership Cost or its importance. Getting it right in planning will save you a massive headache later.
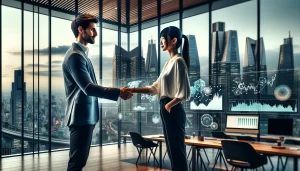
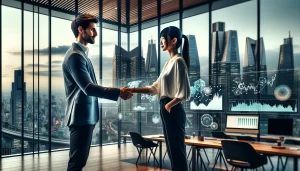
When Data Science Meets Domain Expertise
In the modern days of GenAI and advanced analytics, businesses need to bring domain expertise and data knowledge together in an effective manner.
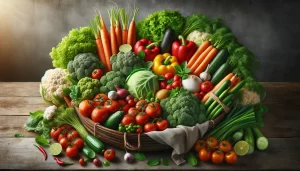
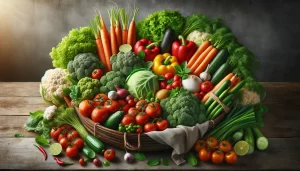
Keeping it Fresh: Don’t Let Your Data Go to Waste
Data must be fresh, i.e. readily available, relevant, trustworthy, and current to be of any practical use. Otherwise, it loses its value.